What are LGA and BGA?
In the domain of electronics LGA and BGA are so important roles. LGA stands for Land Grid Array. It is a type of electronic packaging technology used for mounting microprocessors or integrated circuits onto a printed circuit board (PCB). In an LGA package, the contacts or pins are located on the device's bottom surface and arranged in a grid-like pattern.
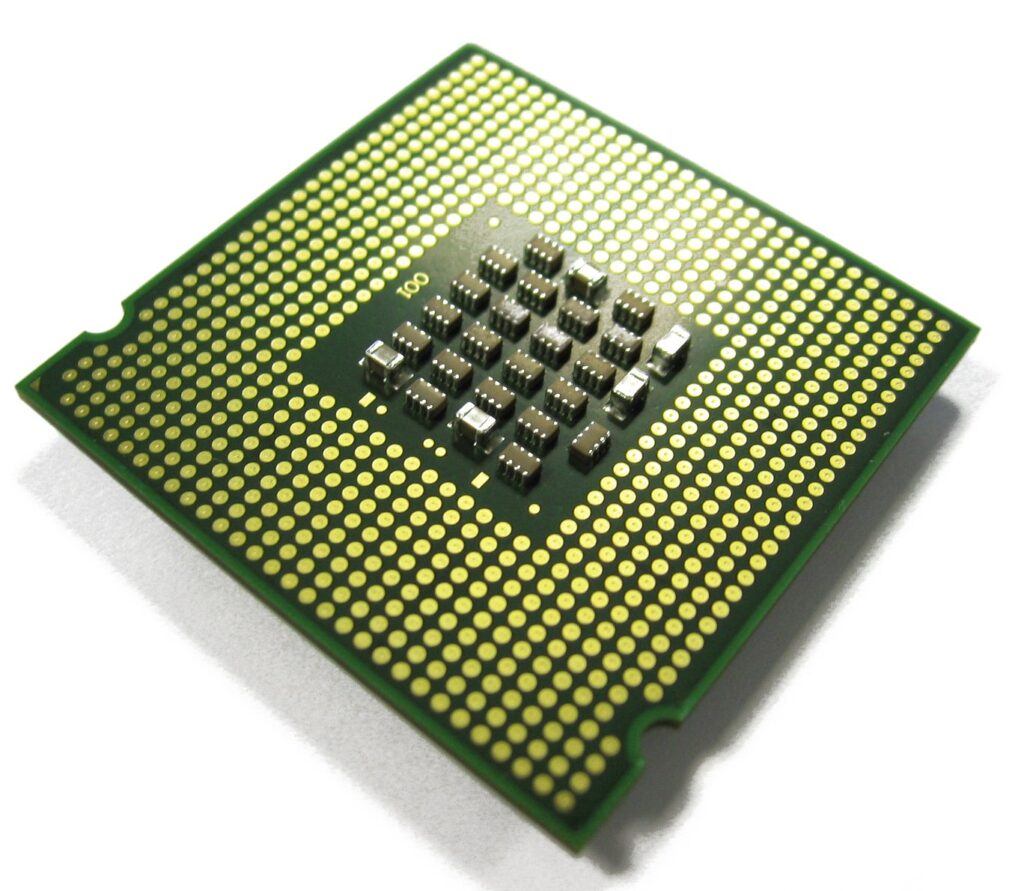
The contacts are designed to mate with corresponding pads on the PCB. That provides the electrical connection between the component and the board.
BGA stands for Ball Grid Array. It is another type of electronic packaging technology commonly used for microprocessors, graphic processors, and other high-density integrated circuits.
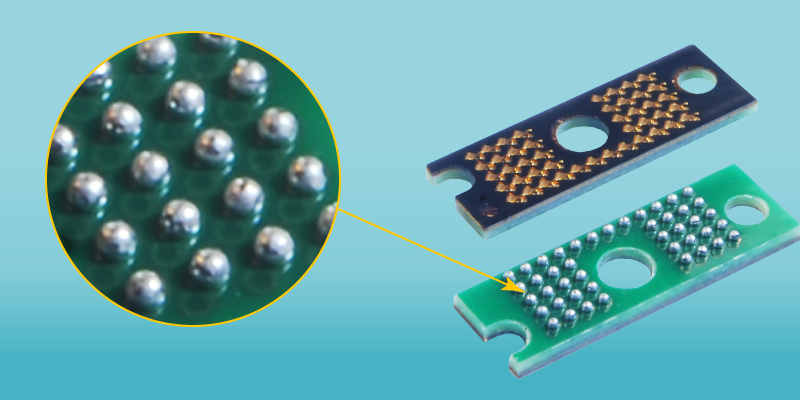
In a BGA package, the contacts are replaced by small solder balls. That is arranged in a grid-like pattern on the bottom surface of the device. These balls provide both the electrical connection and mechanical support for the component.
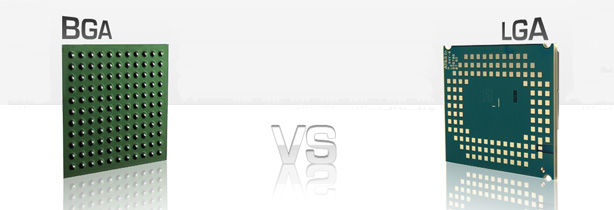
In summary, they are two types of electronic packaging technologies. Mainly used to mount components onto a printed circuit board. While LGA uses pins or contacts to provide the electrical connection, BGA uses small solder balls.
The Difference between LGA and BGA
The primary contrast between these two lies in their method of establishing electrical connections.
In an LGA package, the pins are located on the device's bottom surface and arranged in a grid-like pattern. These pins typically have a flat surface on the bottom, which contacts the corresponding pads on the PCB. The contacts are designed to provide both electrical and mechanical connections between the component and the board.
In contrast, a BGA package uses small solder balls arranged in a grid-like pattern. These solder balls provide both the electrical connection and mechanical support for the component. Components on a printed circuit board are effectively fastened in place through reflow soldering. It is an involved process that requires precise temperature control to melt solder balls and form strong bonds.
Here are some other differences between LGA and BGA:
- Pitch: The pitch, or the distance between the center of each contact or ball. It is typically smaller for BGA packages than for LGA packages. This allows for higher pin or ball density, which means that more connections can be made in a smaller space.
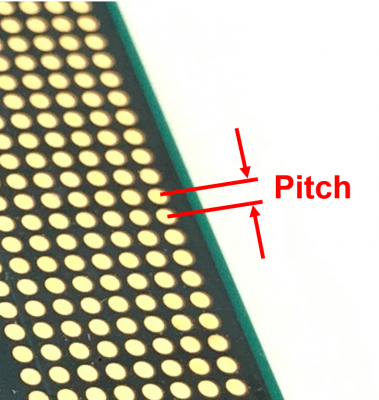
- Thermal properties: BGA packages tend to have better thermal properties than LGA packages. This is because the solder balls provide a more uniform and efficient heat transfer path.
- Repairability: BGA packages can be more difficult to repair or replace than LGA packages. This is because the solder balls are typically hidden underneath the component and require specialized techniques of removal.
- Cost: BGA packages can be more expensive to manufacture than LGA packages. This is due to the additional process steps required for attaching the solder balls.
LGA: Advantages and Disadvantages
Advantages of LGA:
- Higher pin count: LGA packages can support higher pin counts than BGA packages. By making them a good choice for complex devices that require a large number of connections.
- Easy inspection: The contacts in LGA packages are visible. Therefore, it's easier to inspect and test the connections for quality and reliability.
- Better mechanical support: The pins in LGA packages provide better mechanical support than the solder balls in BGA packages. This can help to reduce the risk of damage to the component during handling or transportation.
- Lower cost: LGA packages are generally less expensive to manufacture than BGA packages. Because they require fewer process steps and materials.
Disadvantages of LGA:
- Limited density: The pins in LGA packages take up more space than the solder balls in BGA packages. This can limit the density of the connections and the overall size of the package.
- Solder joint fatigue: The solder joints between the LGA package and the PCB can experience exhaustion over time due to thermal cycling, vibration, and other stresses, leading to reliability issues.
- Difficult to repair: LGA packages can be difficult to repair or replace if one of the pins is damaged or broken. Because the pins are located on the underside of the component and require specialized tools and techniques to access.
- Limited thermal performance: The pins in LGA packages can create a bottleneck for heat dissipation. Because they limit the surface area available for thermal transfer between the component and the PCB.
Overall, LGA packages are a good choice for applications that require a high pin count, easy inspection, and lower cost, but they may not be suitable for applications that require high-density connections, good thermal performance, or easy repairability
BGA: Advantages and Disadvantages of BGA
Advantages of BGA:
- Higher pin density: BGA packages support a higher pin density than LGA packages, which makes them a good choice for components with a large number of connections.
- Improved thermal performance: BGA packages have better thermal performance than LGA packages, as the solder balls provide a more efficient and uniform heat transfer path between the component and the PCB.
- Better signal integrity: The shorter interconnect lengths in BGA packages help to minimize parasitic capacitance and inductance, which can improve signal integrity and reduce noise.
- Small size: BGA packages are typically smaller in size than LGA packages, which allows for more compact designs and higher component density on the PCB.
Disadvantages of BGA:
- Difficult inspection: BGA packages are difficult to inspect visually, as the solder balls are located on the underside of the component and cannot be seen directly.
- Difficult repair: BGA packages are more difficult to repair or replace than LGA packages, as the solder balls are hidden underneath the component and require specialized tools and techniques to remove them.
- Higher cost: BGA packages are generally more expensive to manufacture than LGA packages, as they require additional process steps and materials for attaching the solder balls.
- Solder joint reliability: The solder joints between the BGA package and the PCB can experience mechanical and thermal stresses, which can lead to reliability issues over time.
When to Use LGA and BGA?
The choice between these two depends on the specific requirements of the application. Here are some general guidelines for when to use LGA vs. BGA:
Occasions to use LGA:
- When the component has a lower pin count: LGA packages are a good choice for components with a lower pin count, as they can provide good mechanical support and easy inspection.
- When repairability is important: LGA packages are easier to repair or replace than BGA packages, as the pins are visible and accessible for repair.
- When cost is a major factor: LGA packages are generally less expensive to manufacture than BGA packages, which can make them a good choice for cost-sensitive applications.
- When the component requires high mechanical stability: LGA packages provide better mechanical support than BGA packages, which can be important in applications where the component is subject to vibration, shock, or other mechanical stresses.
Occasions to use BGA:
- When the component has a high pin count: BGA packages are a good choice for components with a high pin count, as they can support a higher density of connections.
- When thermal performance is important: BGA packages have better thermal performance than LGA packages, which can be important in applications where the component generates a lot of heat.
- When signal integrity is a concern: BGA packages have shorter interconnect lengths than LGA packages, which can help to minimize parasitic capacitance and inductance and improve signal integrity.
- When the small size is important: BGA packages are typically smaller than LGA packages, which can be important in applications where space is limited.
When it comes to selecting the right package type for an application, designers should consider all factors and carefully weigh up the pros and cons between LGA and BGA. Expert judgment is key in making sure you select one that meets your exact requirements.
Applications LGA and BGA Components
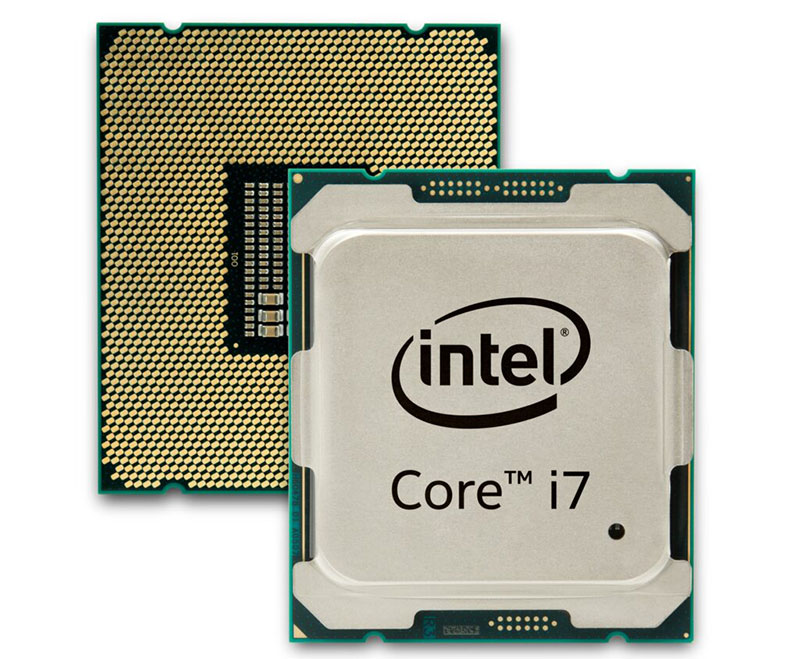
Examples of LGA components:
- Intel Core i7 Processor: Many Intel Core i7 processors use LGA packages, such as the LGA 1151 socket type.、
- DDR4 Memory Modules: Many DDR4 memory modules use LGA packages, such as the LGA 3647 socket type.
- Ethernet Controllers: Many Ethernet controllers use LGA packages, such as the Intel I210 Ethernet controller.
- Power MOSFETs: Many power MOSFETs use LGA packages, such as the Infineon OptiMOS.
Examples of BGA components:
- Graphics Processing Units (GPUs): Many graphics processing units (GPUs) use BGA packages, such as the Nvidia GeForce RTX 3090.
- System-on-Chip (SoC) Processors: Many system-on-chip (SoC) processors use BGA packages, such as the Qualcomm Snapdragon 888.
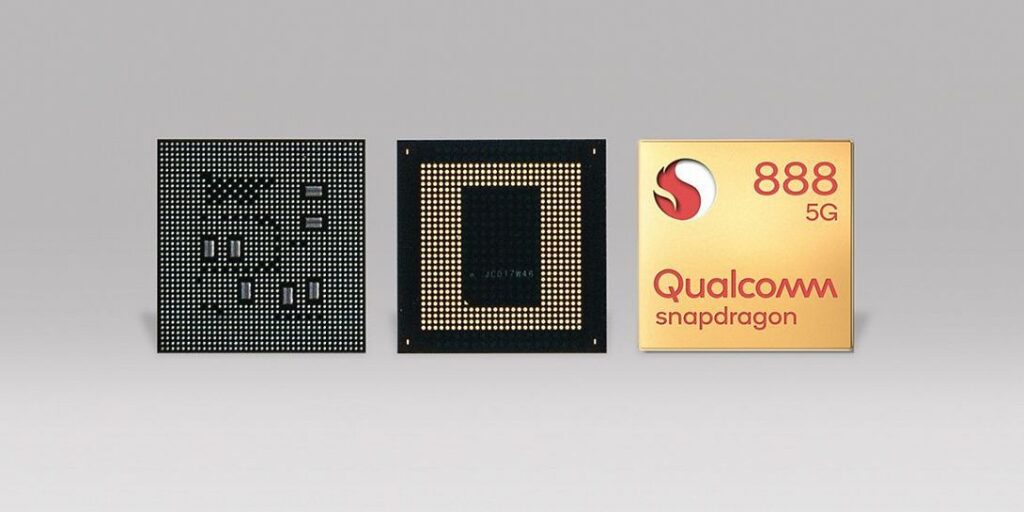
- Field-Programmable Gate Arrays (FPGAs): Many FGPGAs use BGA packages, such as the Xilinx Virtex UltraScale+.
- Memory Controllers: Many memory controllers use BGA packages, such as the Cypress HyperBus Memory Controller.
Note that these are just a few examples, and there are many other components that use LGA and BGA packages. The specific package type used for a given component depends on factors such as pin count, thermal performance, signal integrity, and cost.
Factors to Consider When choosing between LGA and BGA
In the world of PC packaging, LGA and BGA are two popular choices. When evaluating which to choose for your project, there are a few key points you'll want to understand from both sides; including package size & structure, compatibility with components, and cost-effectiveness.
- Pin count: Pin count is key when deciding between LGA and BGA packages. If the component you are designing requires a large number of pins, then the best is the BGA package. However, if fewer pins are needed, an LGA would probably fit the bill.
- Thermal performance: BGA packages are typically better at dissipating heat than LGA packages. Those can be important in applications where the component generates a lot of heat. The thermal performance of the package will therefore be an important consideration, particularly in high-performance applications.
- Signal integrity: BGA packages have shorter interconnect lengths than LGA packages. Those can help to minimize parasitic capacitance and inductance and improve signal integrity. If signal integrity is a critical factor in the application, BGA packages may be the preferred choice.
- Mechanical stability: LGA packages provide better mechanical support than BGA packages. Those can be important in applications where the component is subject to vibration, shock, or other mechanical stresses. The mechanical stability of the package will therefore be an important consideration in some applications.
- Cost: LGA packages are generally less expensive to manufacture than BGA packages. It can make them a good choice for cost-sensitive applications. The cost of the package will therefore be an important consideration in many applications.
- Size: BGA packages are typically smaller than LGA packages, which can be important in applications where space is limited. If a small package size is important, BGA packages may be the preferred choice.
- Repairability: LGA packages are easier to repair or replace than BGA packages, as the pins are visible and accessible for repair. If repairability is an important consideration, LGA packages may be the preferred choice.
Conclusion
In conclusion, LGA and BGA packages are both widely used in electronic components and have their own advantages and disadvantages. LGA packages provide better mechanical support and are generally less expensive, while BGA packages have better thermal performance and signal integrity, and are typically used for components with a higher pin count. When choosing between LGA and BGA packages, designers should carefully consider factors such as pin count, thermal performance, signal integrity, mechanical stability, cost, size, and repairability, depending on the specific requirements of the application. Ultimately, the right package type will depend on the trade-offs that need to be made between these different factors.